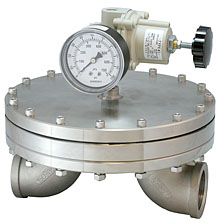
Line size 1.5″ to 4″
SS316, PVC or Anodized Aluminum
Max Pressure of 150 psig / 10 bar(g)
Max Cv of 160
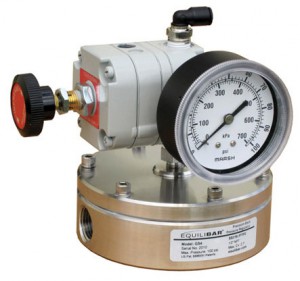
GS Series
Line size 1/4″ to 1″
SS316L, Anod Alum, PVC, PEEK, custom
Max Pressure of 2500 psig / 172 bar(g)
Max Cv of 8.5
How the Equilibar Back Pressure Regulator Works
The internal operation of the Equilibar regulator can be seen in the cross section diagram at right. The diaphragm is the only moving part and acts as the regulator by directly sealing against the internal orifices. The result is instantaneous control keeping the inlet process pressure in tight equilibrium with the pilot regulator
Advantages of Using Equilibar BPRs
Easiest Control Loop
The diaphragm inside the Equilibar back pressure valve is its own closed loop system. The precise 1:1 pressure balance maintained by the diaphragm means that the Equilibar valve will automatically modulate the flow rate to keep the upstream pressure matched to the pressure setpoint. A complicated feedback regulator or hard to tune PID loop is not required
Accurate and Stable Back Pressure Control
The diaphragm inside the Equilibar is frictionless and sensitive to very small changes in the upstream pressure. This diaphragm compensates for system changes automatically and immediately to keep the pressure matched to the pilot pressure.
High Speed Response
The diaphragm is loaded with a compressed gas pilot signal. This allows the diaphragm to respond to changes in the upstream pressure or flow rate within 10mS. The compressed gas on the pilot does not inhibit or dampen the diaphragm’s ability to respond quickly.
High Flow Rate Turn Down Ratio
The Equilibar back pressure valve controls pressure using a multiple orifice design. As the flow rate increases or decreases more or fewer orifices will be brought in to play by the action of the diaphragm. Only one orifice might be required to modulate for very low flow rates while multiple orifices will be used when higher flow rates or surges in the flow occur. Flow rate turn down ratios of over 100,000:1 are achievable.
High Pressure Turn Down Ratio
The diaphragm inside the Equilibar regulator is flexible and strong as it is manufactured from modern polymers. This diaphragm allows the valve to control back pressure over a very wide range. For example, a 1000 psi control valve could be expected to control pressures as low as 25 psi while maintaining accuracy.
The Definition of Back Pressure Control Valves and Regulators
The term back pressure control valve and back pressure regulator are often used interchangeably. The Equilibar valves shown on this page are also referred to back pressure regulators on the rest of this site. However, Equilibar uses the term back pressure valve to describe regulators which are 1.5 inch size or larger while reserving the term back pressure regulator to describe products that are smaller than 1.5 inches.
Flow Control using Back Pressure Control Valves and Regulators
Equilibar back pressure regulators and valves can be used to control flow across a wide range of flow rates using closed loop automation. Equilibar valves are being used for flow control in challenging operations such as extremely wide Cv ranges, low DP or high DP, multiphase or supercritical flow, continuous flow and sanitary applications.
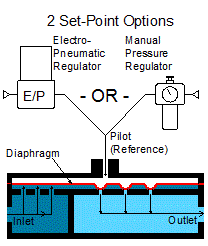
Cross-sectional diagram of an Equilibar back pressure regulator
An Equilibar electronic pressure regulator can directly command the pilot of the Equilibar® back pressure valve with no PID, tuning, or sluggish performance. The Equilibar is capable of handling flow rate variations up to 1000:1 compared to 15:1 for most traditional control valves.