NOTE About this page
Equilibar valves are used today to solve many complex flow control applications. This page shows the early learnings of applying an Equilibar valve to control flow and is retained for historical archive purposes.
For the latest information about Equilibar flow control valves
visit our updated flow control page.
The following flow control schematics provide examples of applications that can be used to provide computer automation of flow rate. There are numerous ways that electronic pressure regulators can be used to pilot dome-loaded back pressure regulators in precision computer automated flow control.
Glossary:
- EPR: Electronic Pressure Regulator (sometimes E/P, I/P)
- DLBPR: Dome-loaded Back Pressure Regulator
- Control Valve: a manual control valve, automated control valve, or fixed orifice used to throttle flow and create a pressure drop
- Aux Supply: a separate gas supply to the EPR, typically air or nitrogen
- Media: process fluid that is being controlled (unlabeled stream on bottom left)
- I: Inlet to EPR
- O: Outlet to EPR
- Ref: reference port that the EPR uses to gauge its pressure against (often open to atmosphere but can be ported to other pressures)
- Exhaust: The port that the EPR exhausts to in order to lower gas pressure
Establishing Fixed Pressure Differential Across Control Valve Using EPR and BPR
In this setup, the reference pressure to the EPR is from media supplied to the control valve, thus allowing the EPR/BPR combination to control the delta pressure (dP) across the control valve. This can be useful for improving the stability and extending flow range of the control valve.
Using Process Media to Supply the EPR
In this schematic, the EPR is supplied with the same gas media that is flowing into the BPR. Optionally, the EPR exhaust can be routed to the output (vent) port of the BPR. A spring bias may also be used.
Porting EPR Exhaust into the BPR Outlet
This flow control schematics depicts supply pressure to EPR from an auxiliary source, while the EPR exhaust is common with the BPR outlet.
Porting EPR Exhaust into the BPR Outlet
Here, a pressure transmitter converts the media pressure to an electronic signal, which commands EPR#1. EPR#1 is used to provide a reference pressure to EPR#2. This is useful when the media is corrosive, hot, or otherwise incompatible with the EPR.
Controlling Density and Differential Pressure at Control Valve
EPR#1 sets the common mode (density) pressure while EPR#2 controls the delta pressure across the control valve.
Equilibar Back Pressure regulators can easily be configured with an electronic pressure controller and a flow meter to deliver excellent flow control across a wide range of flow rates.
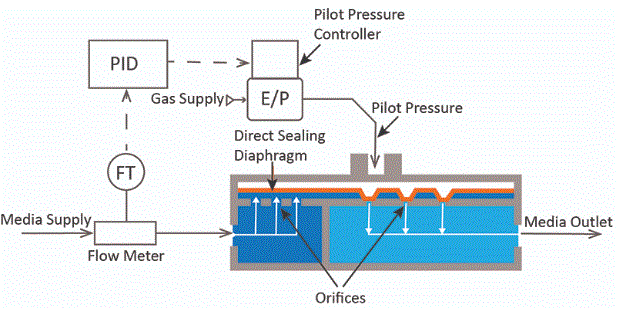
schematic of flow control loop with Equilibar control valve