What is NPSH? and how does NPSH affect single-use bioprocessing design?
NPSH is the measure of head pressure available at the pump suction (inlet). If NPSH is too low, cavitation may occur and if NPSH is too high, it may result in unwanted flow-through.
Single-use pumps are used to deliver fluids from a variety of sources, including break bags, header drops, and buffer totes. Sometimes the supply pressure from a header drop can be high, or an elevated tote storage can add several psi to the inlet pressure of these pumps. High feed pressures to most single-use pumps can cause flow-through even when the pump is off. It can also result in less accuracy in the low flow range of the pump. In some system configurations, feed pressures <1 psi can result in this phenomenon, and may be common in single use manufacturing settings.
The greater the supply pressure to the pump, the more magnified this “push through” flow phenomenon becomes, limiting pump turndown, decreasing dosing accuracy and ultimately reducing dilution accuracy. High Inlet pressures can also add to the head pressure on a pump, putting the downstream system at risk for bursting.
How to compensate for high NPSH
To prevent high NPSH, the bioprocessing industry has attempted to use stainless steel pressure reducing valves (PRVs) or single-use pinch valves to reduce the pressure of incoming fluids. These two options have led to less than optimal results with pump cavitation still occurring at times. In some instances, there is not yet a clearly defined solution. Some systems may not tolerate a single use pinch valve due to slow response times, leading to no identified solution for single use systems, until now with Equilibar’s SDO product.
Equilibar has discovered that using their patented multiple orifice single-use back pressure regulator (BPR) on the outlet side of a pump is a more effective way of mitigating these problems caused by NPSH. If the BPR is set at a value greater than the supply pressure to the pump (commonly called NPSHa), the pump will operate with the right differential pressure to drive flow and the flow-through problem will resolve. The Equilibar BPR is dome-loaded and controlled by a secondary standard pressure regulator called a pilot regulator. The BPR can be controlled manually or electronically, depending on the application requirements.
Application Highlight – Using Equilibar SDO to control NPSH in buffer delivery
In the example below, an Equilibar SDO single use back pressure regulator is positioned after the buffer delivery pumps and inline mixer to help control differential pressure in the diaphragm pumps.
Positioning the SDO back pressure regulator downstream of the diaphragm pumps and static mixer helps several key aspects of the gradient elution system performance.
- Firstly, the NPSH push-through flow issue can be avoided by setting the upstream pressure of the SDO valve greater than the incoming pump suction pressure. This ensures that the pump’s fluid power can generate flow against a higher head pressure, resulting in proper check valve performance in the diaphragm pump.
- Second, even when the pump is off, the setpoint of the Equilibar SDO regulator will prevent any flow through the system.
- Additionally, the upper and lower flow ranges of the pump will more accurately dose buffer to the column, which should improve performance on the gradient profile and increase precision delivered by this two pump solution.
- The SDO valve is capable of handling any flow range generated by the pump, making it a versatile solution to pair with any pump for manufacturing needs. Read here how an Equilibar valve with extremely wide flow range capabilities can help in sanitary processing.
More benefits to using an Equilibar single-use valve for buffer delivery in bioprocessing
Beyond NPSH issues, the SDO valve also helps dampen pump pressure fluctuation which often arises with positive displacement pumps used in buffer delivery. Dampening pulsations will stabilize pump flow performance and help improve flow meter accuracy due to a normalized pressure environment.
These added benefits of better flow stability, increased pump performance, pulsation dampening, and flow meter accuracy create a more stable, precise system. This will lead to improvements in system function, increasing process efficiency and product yield during the ion exchange phase in chromatography.
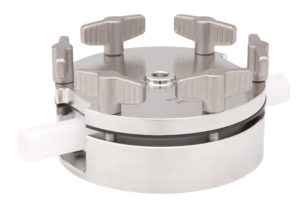
Equilibar SDO6 Single Use back pressure regulator
Request a Quote Download Brochure
FAQ about NPSH
How do I get my pump to shut off?
A pressurized supply may explain why a pump will not go to zero flow. Many pump designs rely on check valves to prevent backflow. If the supply to the suction side of these pumps is pressurized, this pressure will act to force both check valves open. Even when the pump is off, pressure will continue to drive flow through the pump. The undesirable continuous flow through a pump can be called bypass flow or leak by flow and is caused by elevation head pressure in a storage tank or by a pump supplied from a pressurized pipe.
One method to improve the low-flow performance of a pump and prevent push-through flow is to install a back pressure regulator on the outlet of the pump. When the back pressure regulator is set to control at a pressure any amount above the pressure on the inlet of the pump, flow will be shut off when the pump is off. When the pump is turned on, the outlet pressure of the pump will rise causing the back pressure regulator to open. The pump speed will control the flow rate.
Why won’t my pump control at low flow rates?
When a pump has a net positive suction head (NPSH, the supply port of the pump always has a positive supply pressure), the media may push through the pump even when the pump is in a low speed or off condition. Attempting to control flow rates lower than the amount being pushed through by the media pressure will not result in a lower flow rate. This creates an inability of the pump to control low flow rates or stop the flow that is always coming through the pump.
How can I improve the low-flow performance of my pump?
Pressure on the supply port of the pump can cause a continuous flow through the pump. This results in poor low-flow pump performance as shown in the first chart at right. Controlling at flow rates lower than the push-through flow can be achieved with a back pressure regulator installed on the outlet of the pump. When the back pressure regulator is set to a pressure just above the pressure on the pump’s inlet, flow will occur only when the pump is on. When the pump is spinning, the outlet pressure of the pump will rise, overcoming the setpoint of the back pressure regulator, and flow will be provided to the system. Flow rates will return to expected values as shown in the second chart at right.
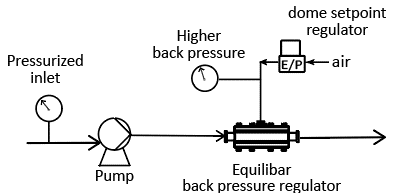
A back pressure regulator is used to stop pump push-through flow
Why can’t I use a pressure regulator on the inlet of my pump?
It appears that regulating the supply pressure to the pump could prevent the incoming media from pushing through the pump and causing continuous flow when the pump is asked for low flow rates or shut off. In theory, this works. In practice, there are two problems with this approach.
The first issue with regulating the input pressure to a pump is that this can cause cavitation. Cavitation can occur when the pressure of the media dips below its vapor pressure at that temperature. The higher the temperature of the media, the more likely cavitation will occur. The lower the media pressure, the more likely cavitation will occur. The pressure regulator must be set to a very low or atmospheric pressure to prevent push-through flow. When the pump speed is adjusted for a higher flow rate, the suction side of the pump must pull from the pressure regulator. Any restriction from the regulator or performance droop will cause a vacuum condition at the inlet to the pump and possible cavitation. This is avoided if the inlet to the pump remains pressurized by the incoming media and a back pressure regulator is used on the pump outlet.
The second issue with using a pressure-reducing regulator on the feed side of a pump is that it is very difficult to reliably set a pressure regulator to zero pressure and have the regulator shut off completely. The regulator’s hysteresis often causes residual pressure to remain on the supply side of the pump. While this may reduce the amount of fluid pushing through when the pump is off, it does not eliminate it in the same way a back pressure regulator on the pump’s outlet will.
Why Installing a Check Valve Will Not Prevent Flow Pushing Through A Pump
A check valve cannot be used to solve the issue of a pressurized supply pushing flow through a pump. While a check valve is often used to prevent backflow, this problem here is excess forward flow through the pumps desired flow direction. Backflow occurs when there is residual pressure on the output of the pump that causes flow backward from the pump outlet to the pump inlet port. Backflow occurs when the output of the pump is pressurized, as will often occur in a lift pump where the elevation of liquid in the lift piping causes backflow when the pump shuts off. However, a check valve will not work to reduce or eliminate flow in the forward direction when that flow is caused by elevated pressure on the supply side of the pump.
Can a Solenoid Valve be Used to Eliminate Flow Pushing Through My Pump?
The short answer is, no, at least not easily. The problem with a pressurized supply pushing flow through your pump is that the push through flow rate may be higher than the flow rate you are asking the pump to deliver. This prevents the ability to control at low flow rates. A solenoid valve may be used to stop the flow entirely, but a solenoid will not allow fluid flow controls below the level of push through flow. In addition, the controls required are more complicated as turning the pump ON when the solenoid valve is OFF can cause damage to some pump types. The better way to stop push through flow and still allow the pump to control at low flow rates is to install a back pressure regulator on the outlet of the pump. The back pressure regulator is adjusted to just exceed the pressure on the suction side of the pump.
Do I even need a pump?
If you have an elevated or pressurized supply to a pump, you already have motive force in the system. You may not need a pump to control the flow rate. The advantages of using a back pressure regulator to control the flow rate are:
- Pulsationless flow. The pulsations of a pump are eliminated.
- Smaller footprint.
- Lower cost.
- Simpler and less expensive maintenance.
- Ability to handle a wider variety of media, chemistries, and temperature ranges.
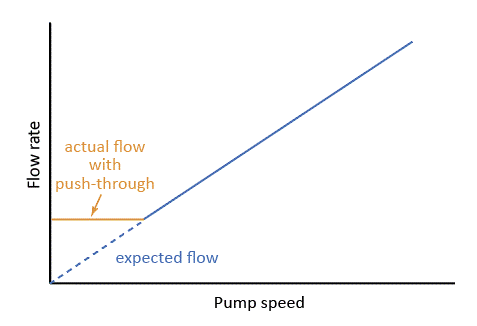
Chart 1 showing unexpected flow rates due to pump push-through flow. Low flow rates cannot be achieved
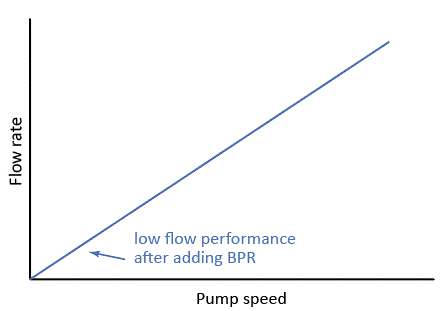
Chart 2 showing good low flow performance now that a back pressure regulator is placed at the pump outlet