For instance, positive displacement pumps, such as lobe or 3-phase diaphragm pumps, are popular in the biopharma and food industries for product transfer and chemical additives. The nature of these pumps, moving a specified volume of fluid for each stroke, typically results in downstream pulsation causing disruptions for the next process. In particular, biopharma filtration and chromatography are easily disrupted when fluid is delivered in pulses. The sensitive resins in the chromatography column can be significantly disturbed due to these pulsations, sometimes damaging the final product. Due to the high costs of biological material, any disruption in the delivery lines is undesirable. Equilibar valves can help.
Equilibar pulsation damping design
Upstream pulsation dampening is a natural behavior of the Equilibar® valve because the upper diaphragm naturally responds to slugs of fluid moving through the valve, keeping upstream pressure constant. The ultra-wide Cv range of the Equilibar valve allows it to keep up with positive displacement pumps to maintain consistent upstream pressure.
Equilibar FD sanitary valves help reduce downstream pulsations in biopharma applications. In addition to the ultra wide Cv range, FD valves include a unique passive dampening design as standard.
The passive pulsation dampening comes from a special insert below the lower diaphragm that absorbs energy through the natural compression of the material. The insert has a unique geometric pattern to allow ample compression while also providing uniform pressure to the underside of the lower diaphragm to maximize its sensitivity. The insert is standard in the Equilibar FDO valve and reduces pulsation amplitude an average of 25%.
For processes with excessive pressure fluctuations downstream of a pump, the Equilibar FD valve has an active damping option. The FDO with Active Damping valve has the same high performance pressure control as the standard FDO regulator. The Active Damping option has a modified bottom cap designed for damping pulsatile flow to accommodate processes with excessive pressure fluctuations due to process equipment such as pumps. This option requires a slightly different process setup so please contact an Equilibar application engineer for more information.
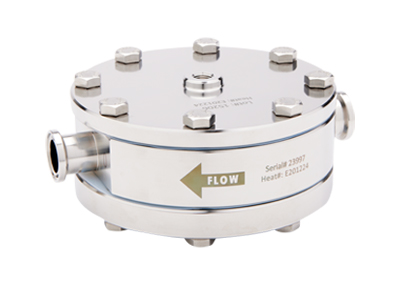
FDO6 3/4″ sanitary valve. Max Cv 4.0
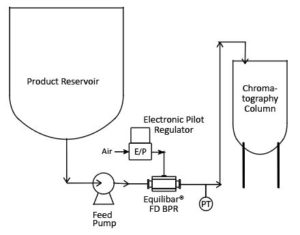
An Equilibar FDO placed downstream of a product transfer pump can reduce pulsations
Looking for pulsation dampening in single use systems?
Learn more about our back pressure regulator technology and how it works.