Culture fluid from a bioreactor is added continuously to the disk stack centrifuge and the centrifugate or centrate, which is the supernatant liquid, is processed continuously. Depending on the design, the solids may be discharged continuously or in batch intervals. Process parameters that contribute to the efficiency of this process are flow rate, or residence time, and back pressure on the centrate line. The centrate back pressure valve helps maintain centrifuge bowl level and creates a hydro-hermetic process to avoid oxidation.
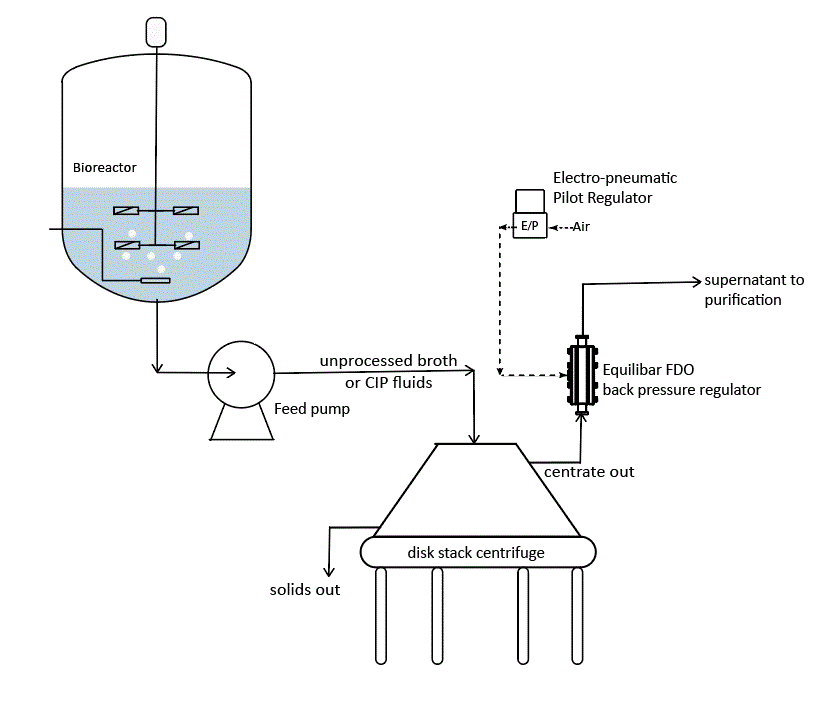
Clarification using a disk stack centrifuge. An Equilibar FDO is controlling centrate pressure
Choosing the right valve for disc stack centrifugate control
Back pressure regulators (BPRs) for disc stack centrifuge centrate control must perform well at standard process conditions as well as robust cleaning conditions. Standard operating conditions are uniquely set to maintain efficient and high-quality supernatant production for a certain cell culture. This is generally a mild temperature and low flow rate. The cleaning process conditions require an increase in flow rate and in temperature and involve caustic and sometimes acidic cleaning solutions. Steam cleaning operates at around 130◦C.
Equilibar FDO sanitary back pressure regulators are a great fit for this application because they can withstand the harsh chemicals and maintain accurate pressure control across the wide Cv process conditions required. The FDO valve features Equilibar’s famed dome-loaded multiple orifice technology delivering instantaneous control, frictionless operation, superior precision, and exceptionally wide flow rate range.
The vibration inherent in centrifuge systems can lead to wear and tear in traditional sanitary valves due to the complexity and large number of connected parts in the stem assembly. This could lead to more frequent maintenance downtime.
The Equilibar FDO regulator is dome-loaded, and a thin supple diaphragm is the only moving part. The pressure on the dome holds the diaphragm in place, sealing the multiple orifices in the FDO body. As fluids flow through the unit, the diaphragm lifts off the orifices to release pressure as the upstream process pressure exceeds the setpoint pressure. The diaphragm maintains precise control by adjusting slightly to process disruptions or setpoint changes.
Contact an Equilibar engineer to discuss your centrifuge application.
Single use back pressure control
The Equilibar® dome loaded multi-orifice valve technology is also available in a single use format. The patent pending Equilibar® SD series back pressure regulators and flow control valves are manufactured using USP Class VI polymers and stainless steel. The polymer body and diaphragms are disposable and are inserted into a stainless steel support housing with wing nut closure for quick and easy assembly.
Contact an Equilibar application engineer for more information.
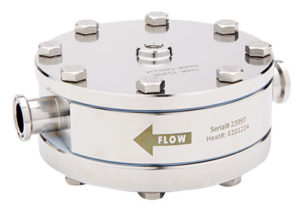
Equilibar FDO6 Sanitary back pressure regulator
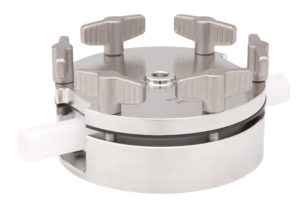
Equilibar SDO6 Single Use back pressure regulator