A typical spring-adjusted pressure sustaining valve is shown in the sketch at right. When fluid pressure on the diaphragm exceeds the spring force, the valve stem lifts and increases flow to achieve setpoint. Pressure is controlled on the inlet port.
Equilibar® back pressure regulators (BPR) are often used as pressure sustaining valves. They have a unique design with a dome-loaded pressure setpoint, a multi-orifice flow path and a single supple diaphragm as the only moving part. This results in higher precision and faster responsiveness for applications where extreme accuracy of pressure control is required.
Request a Quote Download Brochure
Pump Pressure Control
A common application for a pressure sustaining valve is in a recirculation loop with a pump. A pump cannot build its discharge pressure unless there is resistance on its outlet piping. A properly sized pressure sustaining valve can create just the necessary amount of resistance to accurately control pump discharge pressure.
The schematic at right shows how an Equilibar® back pressure regulator (BPR) can perform this pressure sustaining function. Typical applications include spraying or dispensing of liquids.
Application Spotlight: Chiller Loop or Cooling Loop
Glycol chiller cooling loops are used frequently in brewing or fermentation chambers and chemical manufacturing plants to control process temperature inside a reactor or tank. Oftentimes the process temperature during production is a delicate parameter that needs to be kept within a strict operating window. In order to keep that temperature in control, the flow and pressure of the cooling liquid through the chiller loop needs to be accurate.
An Equilibar BPR can be used to control pressure of the chiller fluid loop, keeping process temperatures at the required setpoint. Using the same principle as the pressure sustaining valve above, the Equilibar BPR can be positioned in the recirculating cooling loop to provide stable chiller supply pressure during changes in demand from the manufacturing process.
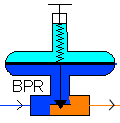
Typical spring-adjusted pressure sustaining valve
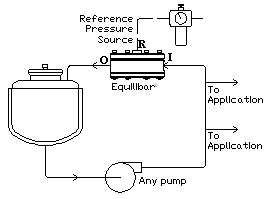
An Equilibar BPR in a recirculating fluid loop controlling pump pressure. Frequently used to control fluid spraying, fluid dispensing and chiller loop applications.
Request a Quote Download Brochure
Equilibar® Back Pressure Valves
Equilibar precision pressure sustaining valves are referred to as back pressure valves or regulators. They work in a different way from traditional valves. They use a fluid pressure on the top of the diaphragm instead of a spring and also use direct diaphragm sealing instead of a traditional valve seat. Their lightning fast response and zero hysteresis give them a real performance advantage over traditional pressure sustaining valves.
If your application requires high precision or has very demanding conditions, the Equilibar BPR may be ideal. Contact us to find out.
2″ Equilibar® precision back pressure valve in Stainless Steel body.