You may not be able to solve your flow control problems by switching to another brand of rising stem valve…
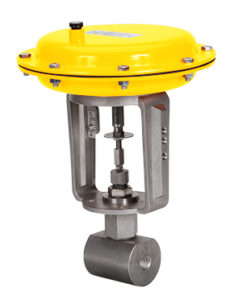
Traditional rising stem valve
Instead, solve your problems with Equilibar’s Automated Flow Control valve
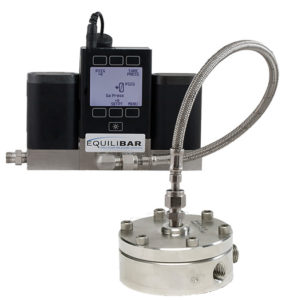
Equilibar Flow Control Valve
Contact Us Download Equilibar Flow Control Brochure
Precision control across an ultra-wide range of flow rates
for gases, liquids and mixed phase fluids.
The Equilibar® advanced flow control valve works in a control loop with an electronic controller and a flow meter. For demanding flow control applications where the supply pressure is largely stable, Equilibar customers have discovered significant benefits including wide Cv range capability, chemical compatibility and multiphase fluid handling.
How it Works in Flow Control
In a flow control configuration, the Equilibar valve works with an electronic pilot pressure controller and a flow meter in a control loop. A proportional-integral-derivative (PID) controller monitors input from a flow transmitter (FT) and adjusts the pilot pressure to bring flow under control. An electro-pneumatic (E/P) pressure controller translates the electronic signal from the PID into a pressure signal for the pilot pressure. Flow is decreased by raising the pilot pressure and increased by lowering the pilot pressure.
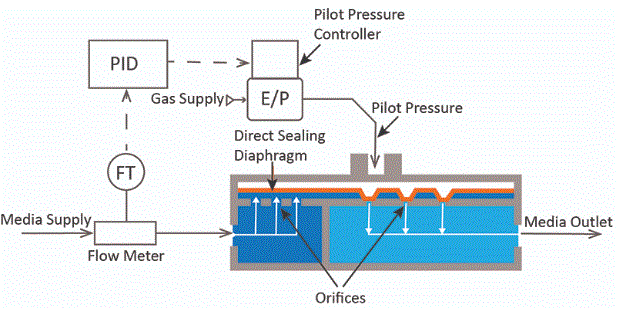
An Equilibar flow control valve works in a PID control loop with a flow meter and an electronic pressure controller.
In this setup, an increase in actuation pressure decreases the flow so the PID control scheme will be set up differently than if using a traditional control valve. In flow control operations with an Equilibar valve, the PID controller must be used in direct mode instead of the more common inverse mode, because pressure must be increased in response to an increase in flow (see graph at right).
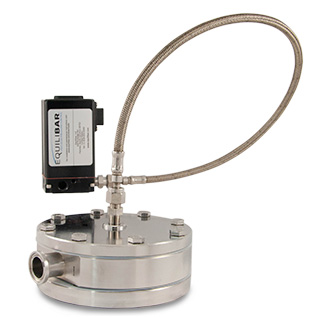
Equilibar FDO sanitary valve with electronic pilot for closed loop Advanced Flow Control
Download a BrochureSpeak to an Engineer
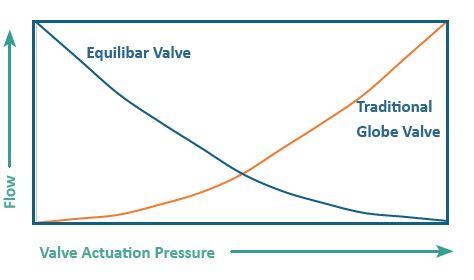
Graph showing opposite responses of a traditional globe valve (red) and an Equilibar valve (blue) in response to actuation pressure
Watch How The Equilibar Advanced Flow Control Valve Works
When to Consider Using an Equilibar Valve for Flow Control
The Equilibar fluid control valve is well suited for demanding application requirements including:
- Flow coefficient (Cv) ranges wider than traditional valves (>100:1)
- Highly corrosive gases and liquids (available in exotic alloy bodies and diaphragms with FFKM)
- High temperature (seals available up to 500ºC)
- Sanitary and biopharmaceutical applications (available with USP Class VI diaphragms)
- Extremely low flow rates (controls Cv down to 1E-9)
- Two-phase, phase-change and supercritical states
- Extremely low DP and extremely high DP
Below is a video showing an Equilibar flow control valve controlling a gas at low flow and high pressure – 100 bar(g) / 1450 psig – at the lab of Pressure Control Solutions, our partners in The Netherlands.
Contact an Equilibar engineer to discuss your flow control application today.
Download a Brochure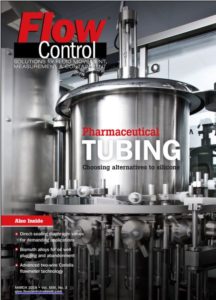
Read our article in Flow control Magazine “Considering innovative direct-sealing diaphragm valves for highly demanding applications”
Valve Specifications