Understanding TMP control for TFF from a fluid mechanics standpoint can help in designing an efficient process. In bioprocessing operations using hollow fiber filters, transmembrane pressure across the filter (TMP) is the key driving factor for all other process variables, from feed flow strategies to permeate makeup flow in diafiltration.
Equilibar Engineer, Ryan Heffner PE, conducted extensive studies in TMP control methods to show how Equilibar® back pressure regulators offer improved precision to TMP control methods for more stable on-target control. His work demonstrated how on-target control impacts TFF unit operation metrics from protein denaturing to operating time.
General concepts of Ryan’s research are outlined below, and a recording of his presentation at BioProcessing International West in March is available upon request. His research and presentation concentrated on the performance of the Equilibar SDO single-use regulator.
The Equilibar FDO stainless-steel regulator has similar performance characteristics and is an excellent choice for multi-use tangential flow filtration applications. Contact us to discuss your TFF system.
Contact Us Request Ryan’s Presentation
Fluid Mechanics Basics in TFF:
Fluid mechanics establishes the critical filtration performance, for which TMP is the main variable. Essential components in a tangential flow filtration system are the feed pump; filter and product interaction; the TMP control device; and the control loop. Component choices and control strategies need to work together to maintain TMP control at an optimal setpoint.
Filter fluid mechanics to consider
Below is a graph of a representative Flux versus TMP curve at two different feed flow rates.
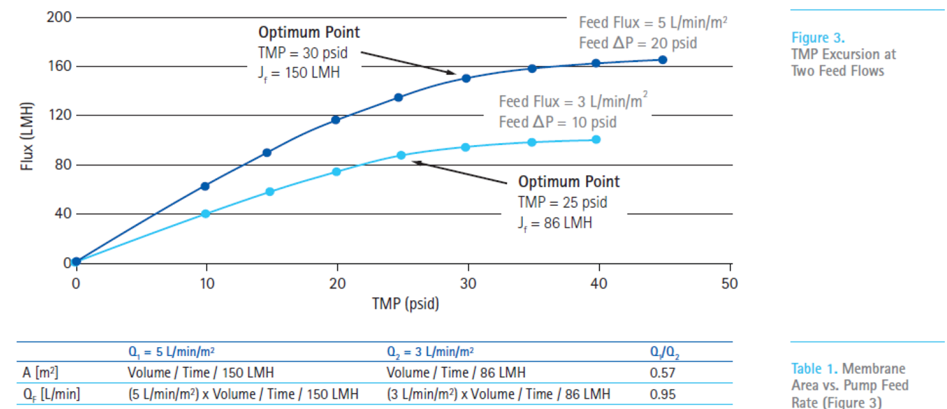
Huter, & Strube, Jochen. (2019). “Model-Based Design and Process Optimization of Continuous Single Pass Tangential Flow Filtration Focusing on Continuous Bioprocessing.” Processes. Available: DOI:10.3390/pr7060317
Points to consider from the curve:
- For most pharmaceuticals, there exists a pressure-dependent and pressure-independent flux point
- Higher TMP accelerates filter membrane fouling.
- Filters have an “optimum” TMP where flux is maximized and membrane fouling is minimized. The goal is to maintain this optimum TMP during the filtration process.
Key System Considerations
- Feed flow should be precisely evaluated to consider shear, gel layer formation, retentate differential, and other variables to properly handle the media entering the filter.
- Consider pump’s fluid behavior – how is flow affected by head pressure, RPM vs flow relationships, and constant RPM flow profiles?
- Impact of feed flow over time and the overall unit operation.
- If single-pass filtration is used, feed flow must also consider flow needs of other unit operations downstream
- Select a TMP control device that can stably control TMP as the process evolves.
- Using a pump or pinch valve requires continuous PID adjustment which may lead to longer settling times and fluctuations as adjustments are made
- Understand how the TMP control device’s behaviors relate to PID control systems. Loop speed and signal aliasing can generate runaway conditions, or require over dampened system monitoring, sacrificing accuracy and responsiveness.
- Ex: Graph below shows how sampling rate in a pulsating wave output can upset the PID loop and destabilize the control.
Experimental Results for 5x Ultrafiltration Unit Operation
TMP performance with Equilibar SDO single use back pressure regulator and standard pinch valve
A lab experiment was set up to explore the benefits of stable TMP control using an Equilibar SDO single use back pressure regulator in comparison to an industry standard pinch valve. The components included a single-use centrifugal pump, Pendotech single-use pressure sensors, a Midikros filter with an SDO or pinch valve in the retentate line at the outlet of the filter to maintain TMP at 10psig with a feed flow of 150 mL/min. Water was the fluid used in this experiment to illustrate component behavior and process impact.
Below are charts showing TMP and permeate flows recorded during the UF operation using the two control devices: Equilibar SDO regulator and a pinch valve. SDO results are in blue and pinch valve results are in orange.
The Equilibar SDO provided much more stable TMP control and consistent permeate flows.
Experimental Results of Benchtop UF/DF Process Using IgG
To link the benefits measured in the water tests to real-world processing, a DOE experiment was conducted at an external lab using a Repligen KMPi Benchtop system. An Equilibar SDO and a pinch valve were used with various pumps (centrifugal, peristaltic, diaphragm) for processing IgG to a 5x concentration target from 2.0 to 10.0 g/L with a 7 DV (diavolume) objective. Each experiment conducted the same UF/DF step while processing time and IgG concentration were monitored.
The graph below shows the IgG concentration over time for each pump / control device combination. It represents product loss over time during the UF/DF operation. The orange lines are results using the Equilibar SDO back pressure regulator while the blue lines are results from the pinch valve. In each case, the SDO showed less product loss than the pinch valve.
The processing time data shows the SDO regulator with any of the pump types saved an average of 18 minutes (out of 117 total) over the pinch valve/peristaltic pump combination, which is a common TFF setup.
Conclusions from TFF experiments using Equilibar SDO
The studies concluded that the selection of components in a TFF system can have a measurable effect on the efficiency of the TMP control. Both experiments point to better TMP control and TFF efficiency using an SDO back pressure regulator than using a pinch valve. The precision TMP control provided by the Equilibar SDO gave very stable permeate flow, resulting in less product loss and faster processing time as compared to a pinch valve. The SDO self-regulates without a PID control loop which can eliminate out of control situations, making it the ideal choice for TFF applications.
Contact Us for more information