Equilibar valves have a unique throat geometry with multiple parallel flow paths that has been shown to avoid cavitation issues (both pitting and noise).
If your flow control or back pressure control application is experiencing cavitation issues, contact one of our engineers to see if our products might be a good fit for your application.
What Causes Cavitation in Pressure Regulators and Valves
All control valves work by creating a pressure drop in a restriction such as a valve seat or an orifice. Typically, fluid flow is accelerated to a maximum velocity in the throat of the valve seat (the vena contracta) where the cross sectional area is smallest. As the fluid decelerates downstream of the throat vena contracta, a portion of that kinetic energy is converted back to potential energy (pressure), causing a partial pressure recovery.
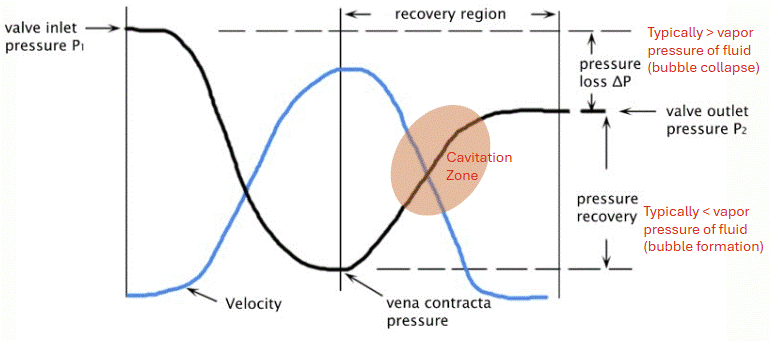
Chart showing reduction in static pressure as velocity is maximized in the valve vena contracta. Image courtesy Jordan Valve.
This pressure recovery is problematic because it provides an environment for the fluid to be briefly at a pressure lower than the valve outlet. Since the outlet pressure may already be near the vapor pressure of the fluid, this localized region of lower pressure near the outlet creates microscopic cavitation bubbles. These bubbles collapse along with the recovered pressure, imparting undesirable energy on valve components. This typically presents itself as noise or vibration in the system, sometimes sounding similar to small rocks or pebbles running through the structure.
Fun fact: this Phys.org article claims that a collapsing cavitation bubble reaches a temperature 4 times hotter than the sun!
Different valve designs have different pressure recovery factors, although all standard valve designs (gate, butterfly, ball) are considered subject to cavitation problems.
Traditional Solutions to Address Valve Cavitation
The valve industry has developed several effective means to avoid the damaging effects of cavitation in common applications such as boiler feedwater and other high pressure water systems. These methods include:
- The use of multiple valves in series–installing a valve or BPR downstream of a control valve protects the upstream valve.
- The use of hardened trims such as Stellite–this approach is commonly used in steam, but is not suitable for chemically corrosive fluid.
- Special trims are available to reduce noise and eliminate cavitation damage.
- Radial Flow trims
- Caged Orifice trims
- Axial Flow Path trims
Many of these designs are mechanically more complex, and these designs are more commonly seen in larger, higher-energy dissipation applications such as municipal water and utility systems. A few models are available in stainless steel body and trim.
Contact Us about Equilibar Anti Cavitation valve
Equilibar as Anti-Cavitation Valve Alternative
Like traditional devices, Equilibar control valves also create a pressure drop by accelerating the fluid to a type of throat near the point where the diaphragm and orifice meet. Unlike traditional valves, however, Equilibar’s direct-sealing diaphragm multiple orifice design features a significantly different geometry of fluid acceleration and deceleration.
Over the past 15 years, Equilibar engineers have specified our BPRs for several thousand different liquid applications. An analysis of customer feedback and returns over this time strongly suggests that our valves are not subject to damage or noise in these applications.
To confirm this hypothesis, we intentionally subjected our 1” GSD8 valve to a warm water recirculation application up to 90 psig that is considered a classic cavitation application. After 40 hours, absolutely no signs of pitting or damage were observed.
Read more about the unique design of Equilibar valves.
Advantages of Equilibar Valves in Cavitating Applications
While other anti-cavitation solutions exist, most are intended for utility applications and larger, high energy dissipating systems. This may not be suitable for highly demanding chemical or research applications that:
- Require materials suitable for highly corrosive applications
- Require very wide flow rate ranges (100:1 or higher turndown ratio)
- Require simpler or more compact designs
- Require sanitary features for food or biopharma applications
Product Details
Equilibar Flow Control Valves Equilibar Back Pressure Regulators
Contact Us
Equilibar engineers are constantly looking for new ways to address demanding customer challenges. If you require a zero cavitation valve and the traditional valve solutions are not a good fit, contact our engineers to discuss whether your cavitating application might qualify for a free trial.
Cavitation-Related Frequently Asked Questions
How do you prevent valve cavitation?
Traditional anti-cavitation methods may employ cavitation-specific trims or gradual pressure drop systems. These methods can be effective in some applications but can oftentimes be large and relatively expensive compared to the natively cavitation free design of Equilibar regulators and valves.
What makes Equilibar Valves Cavitation-Free?
The unique multi-orifice flow path of the Equilibar valve creates a significantly different geometry for fluid acceleration, such that cavitation is avoided
Why should cavitation be avoided?
Cavitation can lead to additional system maintenance and downtime. Since cavitation tends to occur within control valves, sourcing a cavitation resistant or cavitation-free regulator can significantly reduce maintenance and downtime system-wide.
What is the difference between cavitation and flashing
Flashing occurs in liquid flow when the downstream pressure of a valve is less than the upstream vapor pressure, causing part of the liquid to change to a vapor. The flow downstream becomes part vapor and part liquid. This is different from cavitation where the flow downstream of a cavitation region returns to the liquid state. Although flashing can potentially damage a valve or piping, it is generally not as severe as cavitation.