Stainless steel foil remains a very good option for very high temperature and high pressure applications. However, for applications requiring ultra low flow control (flow coefficient Cv less than 1E-3), the polyimide diaphragm appears to be the most promising candidate.
We realize that this material may be unfamiliar to our customers as a diaphragm material, so we are providing this page to summarize the available information and test data.
Performance Assurance:
If you purchase an Equilibar Research Series regulator with a polyimide diaphragm and find it to be unacceptable for your application within six months, we will provide you with an alternate diaphragm material at no charge. If we are not able to satisfy your application, we will refund your purchase price. Our objective is to identify a sensitive and robust diaphragm solution for every application.
Material specification:
- Polyimide diaphragms with thickness of 1, 2, and 5 mil are Kapton HN.
- Polyimide diaphragms greater than 5 mils are formed from DuPont Kapton films which are reported to be extremely similar in properties to the HN formulation.
Published Information
DuPont’s Summary of Kapton® Properties is the primary technical resource available for materials formed from Kapton film.
- Polyimides have the highest service temperatures of the available polymer families.
- Kapton® has excellent chemical resistance and is compatible with all known organic solvents. Though it has resistance to many acids and bases, exposures to strong acids and bases requires further investigation.
- DuPont reports that Kapton is used in some applications up to 400ºC (752ºF)
- Kapton retains approximately 60% of its tensile strength at 200ºC, and 75% of its tensile strength at 100ºC.
- Although there is no significant weight loss seen in Kapton films exposed long term to 400ºC applications, there is a slow degradation of tensile strength when exposed to very high temperatures in the presence of air (oxygen). At 325ºC, DuPont reports a 50% loss of tensile strength of a 1-mil sample after 300 hours. It is presumed that a 20-mil sample would experience much slower oxidative strength degradation, though this needs to be demonstrated.
Equilibar Internal Testing
Our internal orifice burst test is a short-term room temperature test. We typically recommend operating pressures for our diaphragms less than 25% of this burst value. For high temperature or other severe service applications, additional derating factors are applied.
The polyimide diaphragm materials exhibit exceptional burst resistance in these internal tests. Although our internal testers go up only to 15,000 psig / 1034 bar(g), burst pressures can be extrapolated by using larger orifices as a proxy for smaller orifices in the Equilibar regulators. Our internal data shows that the 20-mil polyimide diaphragm has a projected burst pressure of 28,000 psig / 1930 bar(g) in our Research Series. This suggest that this material can be used up to our 5,000 psig / 344 bar(g) limit in normal applications, with a limit of 3,000 to 4,000 psig / 206 to 275 bar(g) for very high temperature applications.
Oven pressure tests at 150ºC and 250ºC show excellent strength retention, even over larger proxy orifices at pressures to 4400 psig / 303 bar(g). More importantly, there is absolutely no indication of wrinkle formation at these high pressure / high temperature combinations.
Our internal performance testing suggests that polyimide diaphragms have excellent sensitivity and low-flow capability. Flow coefficients down to approximately 1E-6 and 1E-7 have been obtained for the pressure range of 1000 psig / 69 bar(g). Not surprisingly, this material ranks significantly more sensitive than stainless steel foils, but not quite as sensitive as PTFE/Glass.
We have conducted an internal test using a 48-hour soak in 30% hydrogen peroxide, with water as a control. Test results showed absolutely no reduction in burst strength with the peroxide or water exposure. A slight mass gain (approximately 3%) was noted in the peroxide sample, but none in the water.
Chemical | Rating | Burst Strength Retention | Weight Gain | Test duration |
---|---|---|---|---|
Acetone | Excellent | 91% (stable) | 9% (stable) | 3, 7, 24 days. 0.002″ / 0.05 mm film |
MEK | Excellent | 91% (stable) | 11% (stable) | |
Denatured Alcohol | Excellent | 92% (stable) | 7% (stable) | |
38% Hydrochloric Acid | Poor | 18% (declining) | 7% (increasing) | |
Water (control) | Excellent | 92% (stable) | 2% (stable) | |
Gasoline (unleaded) | Excellent | 96% (stable) | 4% (stable) | 44 day 0.002″ / 0.05 mm sheet |
Diesel fuel (commercial) | Excellent | 99% (stable) | 2% (stable) | |
Toluene | Excellent | 94% (stable) | 13% (stable) | |
1M HCL (pH 1.2) | Excellent | 98% (stable) | 2% (stable) | |
1M NaOH (pH 12.6) | Poor | 73% (declining) | -27% (dissolving) | |
30% Hydrogen Peroxide | Excellent | 100% | 3% | 48 hour 0.020″ / 0.5 mm sheet |
- Overview of Equilibar back pressure regulators
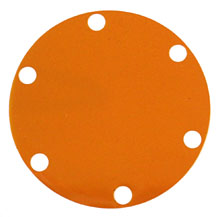