Comparison of Equilibar Control Valves and Traditional Control Valves
While Equilibar® valves inherently function as back pressure regulators controlling pressure upstream of their inlet, replacing control valves is a common use case for Equilibar technology. There are many different benefits to the Equilibar valve design when compared to traditional control valves, though these advantages vary depending on the specific use case.
First, we should define what a control valve is and how that differs from a regulator.
What is a control valve?
A “control valve” is an umbrella term for any valve which allows for control over the size of the fluid passage as a means of controlling flow, pressure, or other process parameters related to flow. By adjusting a positioner or knob, the cross-sectional area (and thus the valve coefficient, Cv) can be changed to modulate the flow through the valve. Engineers often refer to the “% open” of a valve – an indication of the openness of the valve as a percentage of its fully opened state.
Control valves are commonly used in closed loop control setups where measurement of a process variable like pressure or flow is relayed to a PID controller, which then sends a command to an actuator or positioner to set a specific “% open” of the control valve. The use of closed loop control schemes like this allows for control valves to be used for a variety of purposes: controlling flow, upstream pressure, downstream pressure, temperature, etc. As such, they’re often used in place of dedicated regulators due to this flexibility of use. Control valves can come in many different forms, including globe, butterfly, ball, pinch and diaphragm valves.
How a pressure regulator works
Pressure regulators work a bit differently, with their Cv being automatically adjusted to maintain a specific pressure setpoint. Generally, a regulator applies the pressure of a controlled fluid against a diaphragm. The diaphragm opposes a compressed spring or other force to obtain a pressure balance with the diaphragm at a certain setpoint. Pressure reducing regulators sense and control downstream pressure, while backpressure regulators sense and control upstream pressure.
How an Equilibar back pressure regulator works
Equilibar back pressure regulators have a flexible diaphragm sealing on multiple orifices. A pilot pressure fluid (usually gas) is applied to the top of the diaphragm to maintain a pressure balance with the process fluid flowing through the Equilibar regulator. As fluids flow through the unit, the Equilibar regulator holds the process pressure equal to the pilot setpoint pressure above the diaphragm. The diaphragm lifts off the orifices to release pressure as the upstream process pressure exceeds the setpoint pressure. When the flow is minimal, only a portion of one orifice will engage to release the pressure. When the flow is high, the diaphragm is pushed up to engage all the orifices. In other words, the Equilibar valve varies its Cv, or its % openness, in response to variations in flow in order to keep the upstream pressure equal to the pilot pressure.
Benefits of the Equilibar valve design over traditional control valves
The simplicity and elegance of the Equilibar design allows for many benefits over traditional control valves like globe valves, butterfly valves, ball valves, etc.
Because it is a back pressure regulator by design, when used for back pressure control, the Equilibar regulator operates without the use of a closed loop control setup that would be required for a control valve. Elimination of this control loop not only eliminates the cost of the additional components like a pressure transducer and PID controller, but also improves the response speed of the valve. With the Equilibar valve, any fluctuation in flow leads to an immediate movement of the diaphragm – the Cv is adjusted instantaneously to keep pressure stable. By contrast, with a control valve in a closed loop control setup, there will always been some inherent delay between the measurement of the upstream pressure, the PID loop determining the command to output, and translating that command signal to adjust the valve Cv. In processes with rapid fluctuations in flow, this longer response time can cause undesirable pressure fluctuations.
For control of all other process variables (flow, downstream pressure, temperature, etc), the Equilibar valve can be used in much the same way as a traditional control valve. Varying the reference pressure on the dome in relation to upstream pressure will raise or lower the diaphragm, effectively setting the % openness or Cv of the valve. To open the valve more, the dome pressure is reduced and to close the valve more, the dome pressure is increased. This results in a flow response vs. actuation curve that is the inverse of what you’d see with a globe valve.
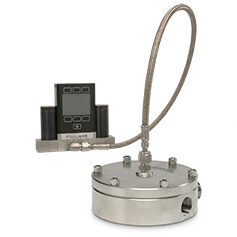
Equilibar 1″ control valve with EPR electronic pilot regulator
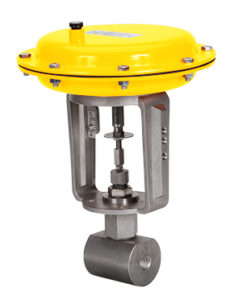
Traditional rising stem control valve
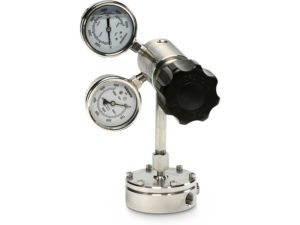
Equilibar back pressure regulator with manual pilot regulator
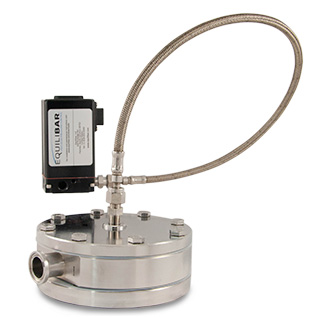
Equilibar FDO control valve with QPV electronic pilot regulator. Perfect for for closed loop Flow Control
3 ways Equilibar outperforms other control valves
Performance
- The multi-orifice design of an Equilibar valve allows for a dramatically larger operating Cv range compared to a traditional single-seat control valve. Equilibar valves are capable of Cv turndown ratios of 100:1 or better. This often allows customers to replace two or more control valves used in parallel with one Equilibar valve.
- Equilibar’s multi-orifice design offers stable control with mixed phase flow. In traditional single seat valves, mixed phase liquid-phase flow can lead to spikes in pressure whenever the flow path is obstructed by a slug of liquid, leaving no path for gas to flow through.
- Faster response time over traditional control valves when used for back pressure control
An article published in the March 2019 issue of Flow Control Magazine describes two customer case studies where an Equilibar flow control valve was used, one with a very wide Cv requirement and the other with multi-phase fluids. In both cases, the Equilibar control valve outperformed traditional control valve designs.
Service Conditions
The simple design of the Equilibar valve allows for easy customization to suit demanding conditions.
- Aggressive Chemistries – Equilibar valves have dramatically fewer internal components, with only the body material, a diaphragm, and set of O-rings. The body material can be easily made from exotic alloys such as Hastelloy or polymers like PEEK and PTFE if needed. Likewise, the diaphragm and O-rings can be made from a wide variety of polymers or elastomers. With traditional single-seat control valves, there are multiple other components that are wetted to the process fluid, making customization for chemical compatibility more difficult
- Extreme temperatures – Equilibar valves can be easily made with all metal seals (a metal diaphragm and graphite gasket or metal c-ring seals) for extremely high temperatures up to 648C. Likewise, the same valves can be used for cryogenic service by changing the diaphragm and O-rings; PTFE, Polyimide, or PEEK diaphragms work great for cryogenic service and the elastomer O-rings can be replaced with spring-energized fluoropolymer jacketed seals. With traditional control valves, operating at extreme temperatures often requires a modified design with a very long stem to prevent the stem seal from experiencing the process temperature.
- Cavitation – The multi-orifice design of the Equilibar prevents cavitation damage. There are no limitations on the pressure drop across the valve when used with liquid. Single seat valves can be easily damaged by cavitation when the pressure drop across the valve is too high.
Maintenance & Cost of Ownership
- Reduced Maintenance Time – The elegant design of the Equilibar valve relies only on a flexible diaphragm and set of O-rings. The valve can be disassembled by simply removing the bolts holding the cap to the body, allowing for all soft seals to be replaced in only a couple of minutes. Once reassembled the valve is effectively “like new” with no additional calibration or tuning needed. Disassembling and reassembling traditional control valves like globe valves can take much longer and getting them to perform the same way they did prior to disassembly can take even longer.
- Cost of Spares – The reduced number of internal components makes the Equilibar spare parts/rebuild kits much cheaper than those for other control valves. Most rebuild kits are less than 10% of the valve’s full price, with the only exceptions being more exotic seals (ie. Kalrez O-rings, metal c-ring seals, exotic alloy diaphragms.)
Watch as Daniel rebuilds a traditional control valve and an Equilibar control valve
Contact an application engineer to discuss your control valve application.
Contact An Application Engineer