On January 20, 2016, Equilibar officially opened its new production floor, doubling the amount of space dedicated to hand assembly of regulators as well as research, testing, and quality control.
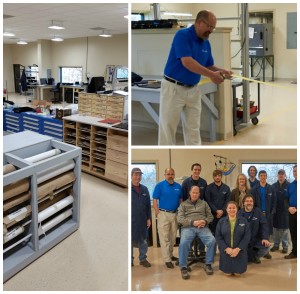
Operations Manager David Reed cuts the ribbon for the new space. Below right, the Equilibar team. Jan. 20, 2016
“We feel fortunate to have experienced remarkable growth during the past few years,” said Equilibar founder and president Jeff Jennings. “We’ve completely outgrown the space we used as a start-up company and look forward to having a spacious, custom-designed area where we can continue developing and improving our back pressure regulators, vacuum regulators and related products.”
The expansion is a major project that has involved months of planning and consultation to ensure that the new space will meet the objectives of increasing capacity for research and new product development, maximizing employee satisfaction, and improving efficiency and environmental impact.
“While our old work space met the needs of a young company, we are looking forward to having a modern, specialized production area that will energize and motivate our talented production team,” Jennings said. “The remodel includes windows that allow natural lighting and a view of the surrounding Blue Ridge Mountains. Connecting to the outdoors is not only aesthetic, but is also proven to encourage job satisfaction and productivity. In addition, placement of work stations, tools and lighting have been carefully reviewed so that our production team’s needs are met and they can work at an optimum level.”
Jennings, who holds multiple patents for fluid pressure control, started Equilibar in 2007 after working as a research engineer for the DuPont Company and other facilities. He was instrumental in the formation of DuPont State Recreational Forest in Western North Carolina and has been actively involved in a variety of conservation and environmental efforts.
“One aspect of the new space that is personally important to me is that it improves our environmental stewardship,” he said. “We’re using all LED lighting, energy efficient windows and a high SEER heat pump to align with our goals of manufacturing as environmentally as possible.”
A new expanded research area will also improve Equilibar’s ability to pursue new applications and products.
“Equilibar stands apart from other companies because of our nimble approach to finding novel solutions to the most complex fluid control challenges,” Jennings said. “The larger research area will further expand our ability to do this.”
Equilibar focuses on custom-designed fluid control products that are hand assembled, inspected and pressure tested for researchers and major industries around the world. Supercritical extraction, vacuum distillation, catalysis research, and renewable energy are a few of Equilibar’s key application areas. The company’s unique technology offers more accurate and precise pressure control compared to standard industrial valve designs.
The company has 12 employees, including five engineers, and collaborates with a variety of local partner businesses to impact the community in multiple ways.
For more information contact inquiry@equilibar.com